Gear Mold Factories: Leading Innovations in Plastic Mold Making
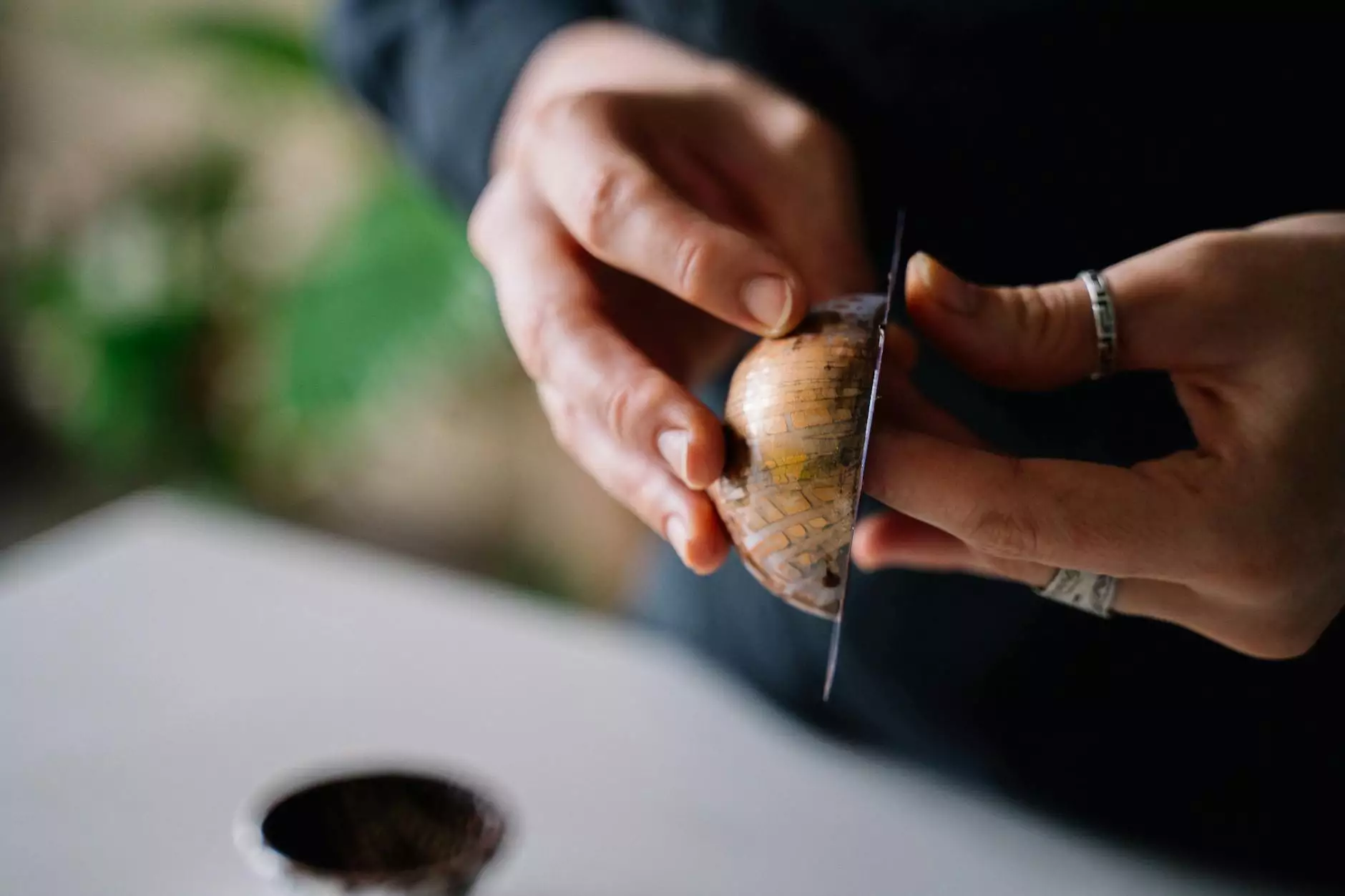
In today's fast-paced manufacturing world, the importance of high-quality gear molds cannot be overstated. Across various industries, from automotive to electronics, precision plastic components are essential not just for functionality, but also for maintaining brand reputation and ensuring customer satisfaction. This article delves into the realm of gear mold factories, with a keen focus on the exceptional work done by Hanking Mould, a top-tier plastic mold maker and plastic injection mould manufacturer.
The Role of Gear Mold Factories in Modern Manufacturing
Gear mold factories are pivotal in the design and production of gear molds that dictate the efficiency and effectiveness of manufacturing processes. Their capabilities encompass a wide range of functions:
- Design: Ensuring that molds are engineered for optimal performance.
- Material Selection: Utilizing advanced materials that provide durability and precision.
- Production Techniques: Implementing cutting-edge technology to foster consistent quality.
- Quality Assurance: Rigorously testing products to meet industry standards.
Understanding the Process of Mold Making
Creating a quality gear mold involves several critical steps. Let’s unpack this intricate process.
1. Conceptual Design
Initially, the journey of a gear mold begins with a conceptual design. Designers collaborate with engineers to create a blueprint that outlines the dimensions, specifications, and materials needed for the mold. This stage is crucial as it lays the foundation for all subsequent activities.
2. 3D Modeling and Prototyping
Using advanced CAD software, engineers develop 3D models of the gear mold. This digital representation allows for precise adjustments and simulations before crafting the actual mold. Often, prototypes are generated using 3D printing technologies to further validate the design.
3. Manufacturing the Mold
The actual manufacturing process might vary, but generally involves:
- CNC Machining: Computer Numerical Control (CNC) machines are utilized to precisely carve the mold from raw materials.
- EDM (Electrical Discharge Machining): This technique is employed for intricate designs that require exceptional precision.
4. Surface Finishing
After machining, molds undergo surface finishing. This enhances the mold’s appearance and functionality, reducing friction and improving the quality of the molded gear.
5. Quality Control
Before production starts, stringent quality checks ensure that every mold meets predetermined specifications. Hanking Mould employs a 100% inspection policy, emphasizing their commitment to excellence.
Why Choose Hanking Mould as Your Gear Mold Factory?
When considering a gear mold factory, Hanking Mould stands out for several reasons:
- Innovative Technology: They utilize state-of-the-art machinery and technology for mold making, ensuring the highest accuracy.
- Experienced Team: The team consists of seasoned professionals with decades of experience in the plastic mold manufacturing industry.
- Custom Solutions: Hanking Mould specializes in creating tailor-made solutions to meet specific client requirements.
- Comprehensive Services: From the initial concept to final production, Hanking provides a one-stop solution ensuring seamless workflow.
The Impact of High-Quality Gear Molds on Industries
High-quality gear molds produced by professionals like Hanking Mould can significantly impact various industries:
1. Automotive Industry
The automotive industry drives innovation, with precise plastic components being critical to vehicle safety and performance. Gear molds from reputable factories contribute to producing gear systems that enhance efficiency and reduce production costs.
2. Electronics Manufacturing
In electronics, every component plays a vital role in overall system performance. Quality gear molds ensure that parts fit perfectly and function as intended, contributing to the durability and reliability of electronic products.
3. Consumer Goods
From appliances to sports equipment, consumer goods rely on molded components that endure heavy use. High-performance molds lead to products that not only last longer but also function better, thereby satisfying customer expectations and promoting brand loyalty.
Future Trends in Gear Mold Manufacturing
The landscape of gear mold factories is evolving rapidly. Here are some anticipated trends that are set to reshape the industry:
1. Automation and AI Integration
The integration of automation and artificial intelligence in the manufacturing process is expected to enhance precision and efficiency while minimizing human errors. Increased automation can lead to faster turnaround times and higher production rates.
2. Sustainability Practices
With growing concerns about environmental impact, gear mold factories are increasingly adopting sustainable practices. This includes using recyclable materials, reducing waste during the manufacturing process, and energy-efficient operations.
3. Advanced Materials
The exploration of new materials, such as bio-based plastics and composites, will open new doors for the design and fabrication of innovative gear molds. These materials often provide enhanced performance characteristics while being eco-friendly.
4. Customization and Rapid Prototyping
As markets demand quicker product development cycles, the ability to offer rapid prototyping combined with customization will become essential. Gear mold factories that adapt to these needs will thrive in a competitive environment.
In Conclusion
In the world of manufacturing, gear mold factories like Hanking Mould are not just service providers; they are integral partners who drive innovation and efficiency. By specializing in plastic mold making and plastic injection mould manufacturing, Hanking Mould has positioned itself as a leader in the industry, committed to excellence through every phase of production. Choosing Hanking means investing in quality, performance, and sustainability, ultimately delivering unmatched value to your manufacturing processes.
As we forward into a future marked by technological advancements and growing industry demands, the role of gear molds will only grow in prominence. Partnering with a reputable gear mold factory is not just beneficial but essential for sustaining competitive advantage in any sector.