Understanding Vacuum System Components: A Comprehensive Guide
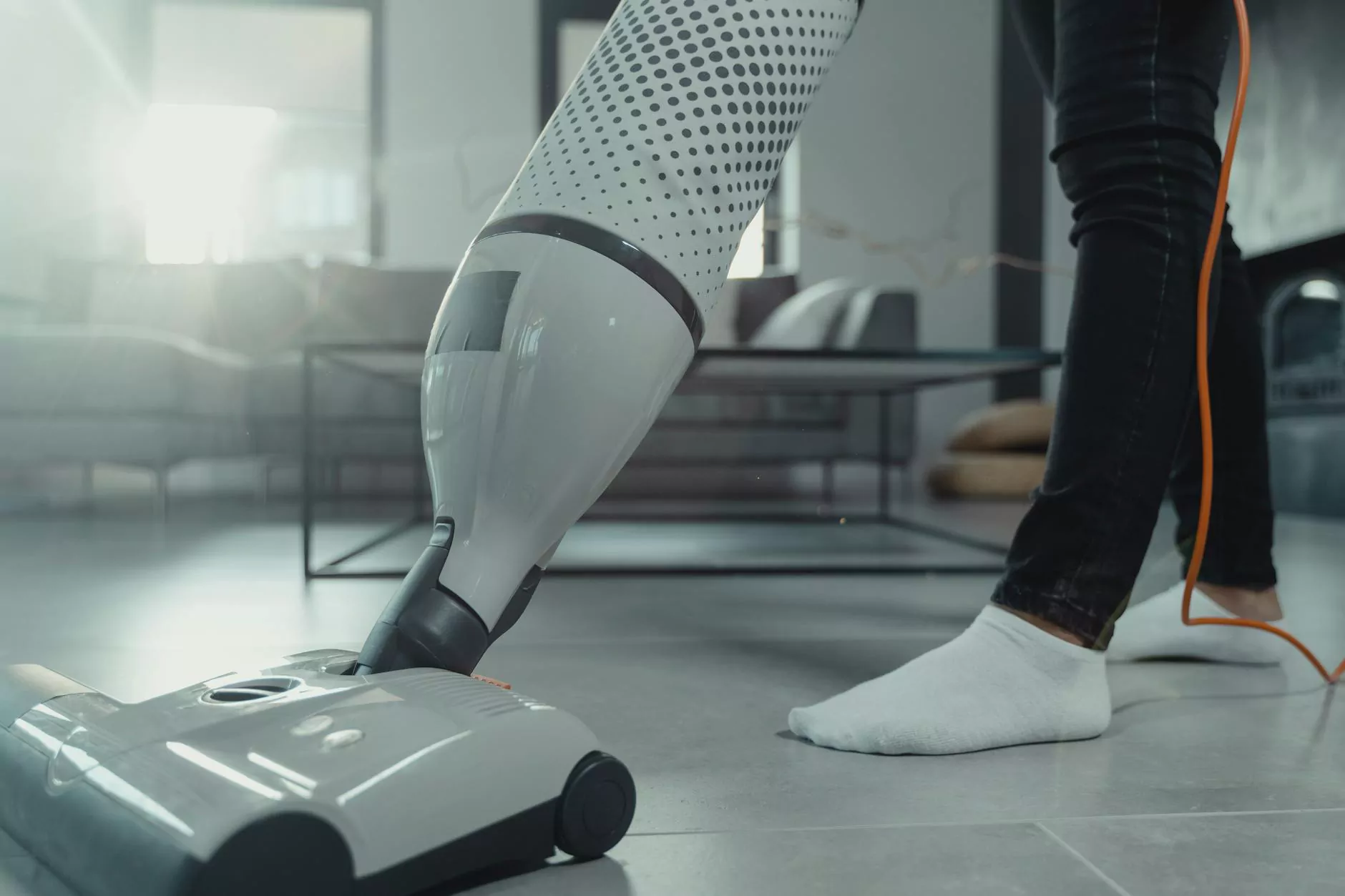
In today’s fast-paced industrial world, vacuum system components play a critical role across various applications. From manufacturing to blow dry/out services, these components ensure operational efficiency and effectiveness in processes that demand precision and quality. This article delves into the various types of vacuum system components, their functionalities, and their importance in contemporary applications.
The Importance of Vacuum Systems in Industry
Vacuum systems are essential in many industries for the following reasons:
- Enhanced Performance: They facilitate processes such as molding, coating, and packaging, ensuring optimal performance.
- Quality Assurance: By removing air and contaminants, vacuum systems improve product quality, particularly in sensitive applications.
- Sustainability: Efficient vacuum systems reduce energy consumption, contributing to sustainable manufacturing practices.
Key Components of Vacuum Systems
Understanding the vacuum system components is essential for leveraging their capabilities effectively. Below are some of the key components:
1. Vacuum Pumps
Vacuum pumps are the heart of any vacuum system. They are responsible for removing air and gases from the environment, creating a vacuum. There are several types of vacuum pumps, including:
- Positive Displacement Pumps: They operate by trapping a volume of gas and then forcing it out of the system. Examples include rotary vane and diaphragm pumps.
- Momentum Transfer Pumps: These pumps such as turbomolecular and diffusion pumps, use high-speed rotating blades to transfer momentum to gas molecules, effectively moving them out of the system.
- Liquid Ring Pumps: These utilize liquid to form a seal and trap gases, making them suitable for various applications.
2. Vacuum Chambers
Vacuum chambers are sealed containers where the vacuum is created. They come in various shapes and sizes depending on the application. Key aspects of vacuum chambers include:
- Material: Most are made from metal or glass and are designed to withstand atmospheric pressure.
- Size: Larger chambers are utilized for bulk processes, while smaller ones are perfect for precise applications.
3. Valves
Valves are crucial in controlling the flow of gases within a vacuum system. They include:
- Gate Valves: Used for on/off control in nitrogen or air lines.
- Isolation Valves: Essential for maintaining vacuum integrity by isolating certain parts of the system when necessary.
- Pressure Relief Valves: These valves prevent over-pressurization by releasing gas when a certain pressure threshold is reached.
4. Gauges
Vacuum gauges are used to measure the pressure level inside a vacuum system. They help in monitoring system performance and ensuring optimal operation. They come in various types:
- Mechanical Gauges: Such as Bourdon tube gauges, which are reliable and straightforward.
- Electronic Gauges: Provide precise readings and often feature digital displays for easy reading.
- Capacitance Manometer: These are highly sensitive and offer accuracy over a wide range of pressures.
5. Filters
Filters are essential for maintaining the cleanliness of the vacuum systems. They prevent particulates from entering the vacuum pumps and damaging the system. Important types of filters include:
- HEPA Filters: These effectively remove small particles, ensuring high air quality.
- Coalescing Filters: Ideal for removing water and other liquid contaminants from gas streams.
Applications of Vacuum System Components in Blow Dry/Out Services
In the realm of blow dry/out services, vacuum system components play a pivotal role in ensuring effective and high-quality results. Here’s how:
1. Enhanced Airflow Control
In professional blow dry/out services, controlling airflow is essential. Vacuum systems help in managing this airflow effectively, allowing for shiny and well-structured hairstyles. The following components are critical:
- High-Performance Vacuum Pumps: Facilitate effective suction for enhanced styling control.
- Pneumatic Systems: These utilize vacuum technology to create soft waves or curls, ensuring desired hairstyles with minimal effort.
2. Hygiene Maintenance
Maintaining cleanliness is crucial in any service industry, particularly in beauty services. Vacuum components ensure:
- Efficient Removal of Hair: Vacuum stripping allows for quick clean-up between clients, enhancing the service flow.
- Contaminant Reduction: Filters integrated within vacuum systems prevent dust and hair particles from circulating in the salon environment.
3. Energy Efficiency
The integration of vacuum systems in blow dry services leads to considerable energy savings. Efficient vacuum pumps and optimized chambers result in:
- Reduced Electricity Consumption: This not only lowers operational costs but also promotes sustainable practices in salons.
- Faster Service Turnaround: Clients benefit from quicker service without compromising on quality.
Maintenance of Vacuum System Components
Regular maintenance of vacuum system components ensures longevity and optimal performance. Here are some maintenance tips:
- Schedule Regular Inspections: Routine checks can identify potential issues before they escalate.
- Clean or Replace Filters: Ensuring filters are clean maximizes airflow and efficiency.
- Monitor Pressure Levels: Utilize gauges to maintain appropriate vacuum levels and optimize conditions.
Conclusion
In summary, vacuum system components are indispensable in achieving quality and efficiency in various applications, including blow dry/out services. A deep understanding of these components fosters better operational practices, ensuring businesses remain competitive and capable of delivering superior services. Investing in quality vacuum systems not only enhances performance but also contributes to sustainability goals, ultimately shaping the future of industries that rely on these technologies. By ensuring consistent maintenance and optimal use, businesses can greatly benefit from the advantages these systems provide.
Understanding the significance and implications of vacuum system components is vital for both service providers and manufacturers. As industries evolve, the integration and efficiency of these systems will only continue to grow in importance.